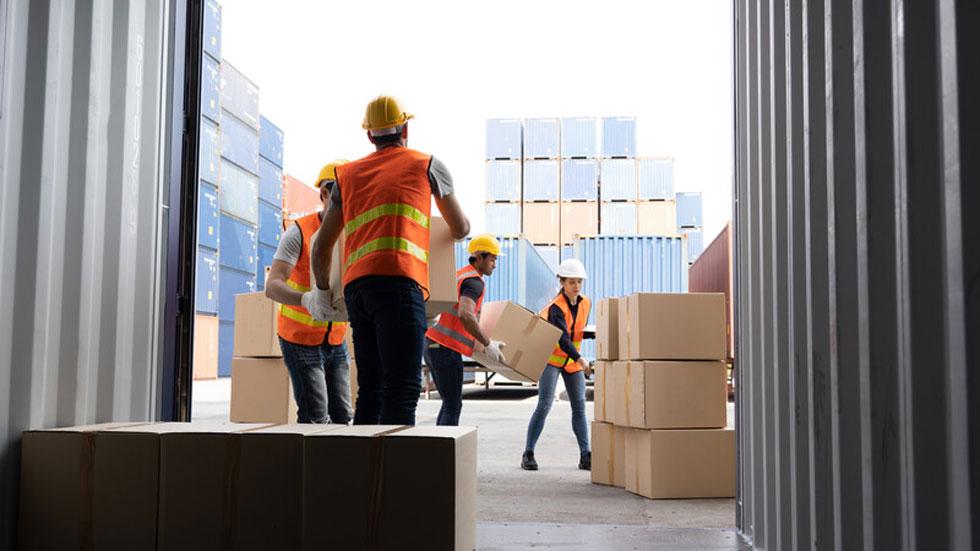
October was a rocky month for the nation’s supply chain. On the first day, about 45,000 workers at 36 U.S. ports went on strike. Although the walkout lasted just three days, it still rattled shippers, retailers, and other supply chain participants.
Later in October, Hurricane Milton barreled through Florida. As Milton made landfall, victims of Hurricane Helene had barely begun recovery efforts in Florida, Georgia, North Carolina, South Carolina, Tennessee, and Virginia.
The dockworkers’ strike and back-to-back hurricanes shed light on ever-looming threats to the supply chain—and their impact on industrial and logistics properties and the REITs that own them. Before, during, and after supply chain disruptions like natural disasters, supplier delays, inventory shortages, and transportation glitches, REITs are well situated to help tenants keep their operations on track.
Experts say the impact of industrial REITs on the supply chain shouldn’t be underestimated. Case in point: Every year, an estimated $2.7 trillion worth of goods flow through distribution centers owned by Prologis, Inc. (NYSE: PLD).
“The U.S. REIT sector owns assets literally across every aspect of our manufacturing and distribution economy, both traditional and digital,” said Scott Robinson, director of the REIT Center at New York University’s Schack Institute of Real Estate.
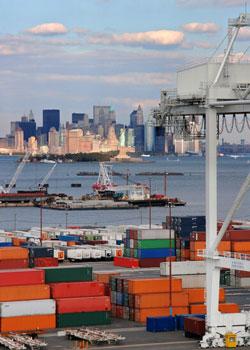
Providing Move-In Ready Space
Although responsibility for a tenant’s supply chain ultimately rests with the tenant, Jojo Yap, chief investment officer at First Industrial Realty Trust, Inc. (NYSE: FR), said the REIT stands ready to aid tenants coping with supply chain breakdowns. As of Sept. 30, First Industrial owned or was developing about 69 million square feet of industrial space in 15 U.S. metro areas.
“As an owner and developer, the most important thing we can do is deliver new buildings on time and ready for occupancy, including installing dock packages and incorporating spec office space,” Yap said. “Similarly, we keep our existing portfolio properties move-in ready to respond to customers’ evolving supply chain needs to drive growth and efficiencies.”
This includes equipping industrial properties with adequately sized truck courts, trailer parking, and dock doors, Yap said, as well as ensuring that construction and permitting requirements are met to enable on-time occupancy.
“Our market leaders and construction teams sit down with tenants to understand how our buildings can best help them meet their supply chain objectives,” he said.
Of course, First Industrial takes those steps before a tenant arrives. Once a tenant has moved in, the REIT’s tenant operations teams can help resolve on-site issues like power outages and mechanical troubles, Yap said.
The assistance doesn’t stop there, though. “Our property management professionals are on call to help tenants however we can to make their building work for them,” he said.
Prologis Goes with the FLOW
Even before the pandemic clobbered the global supply chain, industrial REITs and other warehouse owners closely monitored supply chain disruptions. But the pandemic heightened the need for the public and private sectors to step up preparation for, and response to, supply chain disruptions.
Toward that end, Prologis participates in a public-private partnership known as Freight Logistics Optimization Works (FLOW). Members of this first-of-its-kind initiative, which launched in 2022, collect and share data about the movement of goods.
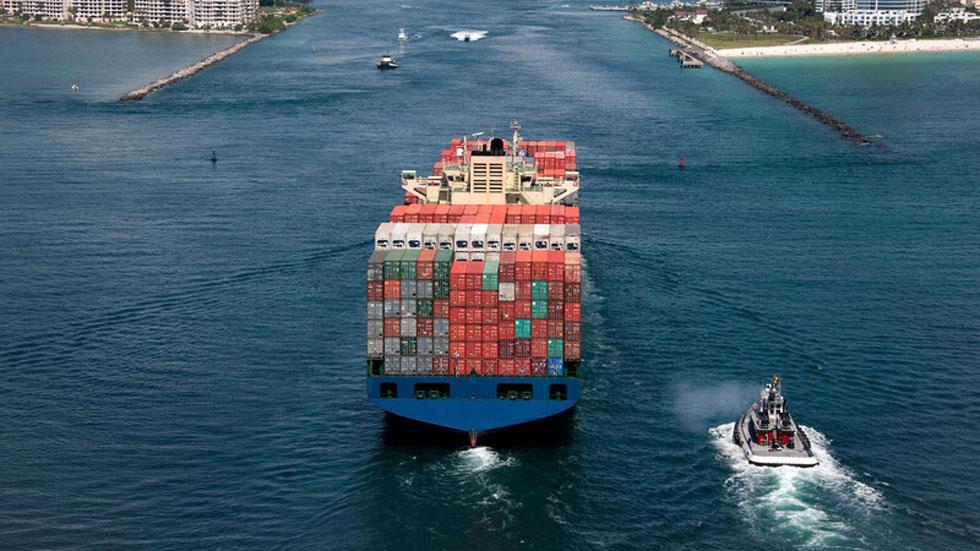
Prologis is one of 18 founding members of FLOW. Chris Caton, managing director of global strategy and analytics at Prologis, sits on FLOW’s executive board.
As of Sept. 30, Prologis owned or had investment stakes in industrial properties spanning about 1.2 billion square feet in 20 countries. Prologis serves about 6,700 customers, including small and medium-sized businesses as well as global brands like Amazon, Home Depot, FedEx, UPS, and Walmart.
Prologis’ efforts to alleviate supply chain disruptions go beyond its membership in FLOW, including:
- Providing flex space to customers when supply chain disruptions happen
- Finding extra warehouse space or container storage space to help customers gear up for and maneuver supply chain disruptions
- Helping customers move goods out of ports in New York and New Jersey before this year’s dockworkers strike. For example, Prologis worked with some East Coast customers to explore short-term options on the West Coast
- Relying on Archipelago productivity software to maintain accurate contact information ahead of October’s back-to-back hurricanes. Prologis is an investor in Archipelago, a data network for insurance brokers and their property customers
- Expanding the Prologis Essentials suite of products and services to help customers quickly set up and scale operations
- Investing $250 million in more than 50 companies whose technology improves warehouse operations
COVID-19 — the biggest supply chain disruptor in recent history — “helped us deepen our understanding of our customers’ operational needs and business goals, which were evolving almost daily during the early days of the pandemic,” said Carter Andrus, chief operating officer at Prologis.
Preparation for supply chain disruptions starts during the construction and development stage for Prologis properties, Andrus said. “Our proactive approach involves assessing natural hazards and climate exposures to make sure that properties are built to withstand potential disasters.”
Beyond Simply Providing Space
As demonstrated by Prologis’ involvement in FLOW, the REIT industry is playing a bigger role in local, regional, and federal policy discussions. This includes weighing in on issues like zoning regulations, building codes, and energy-generating capacity, NYU’s Robinson said.
“Gone are the days when REITs simply provided space,” he said. “The REIT sector is sizable and high profile enough to tactically take a proactive role in their communities.”
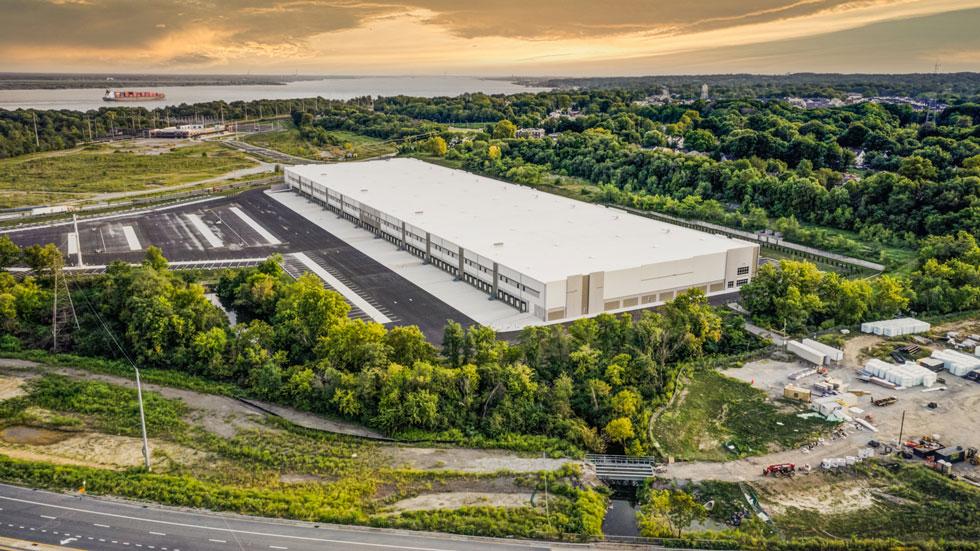
Logistics expert Gregory DeYong, associate professor of operations management at Southern Illinois University in Carbondale, offered similar observations.
Supply chain participants, like industrial property owners, can be “active partners” in planning for and responding to supply chain disruptions, DeYong said. In fact, he believes industrial landlords that offer backup options amid supply chain interruptions deliver a valuable service to tenants.
“I think it is important for facility owners to consider how to market themselves not just as a primary provider, but also as an emergency resource. This may require a high level of responsiveness, but profitability of these services can also be high,” DeYong said.
The ‘Rollercoaster’ of Supply Chain Resilience
To stay on top of supply chain issues, Prologis recently surveyed more than 1,000 business executives, which found that two-thirds of business executives in the U.S., UK, and Germany said they lose sleep over supply chain issues. Economic instability, shifting customer demands, and climate challenges inflame these issues, according to Prologis.
Executives questioned for the survey cited artificial intelligence, automation, “intelligent” data analytics, and sustainability as the primary keys to shoring up supply chain management.
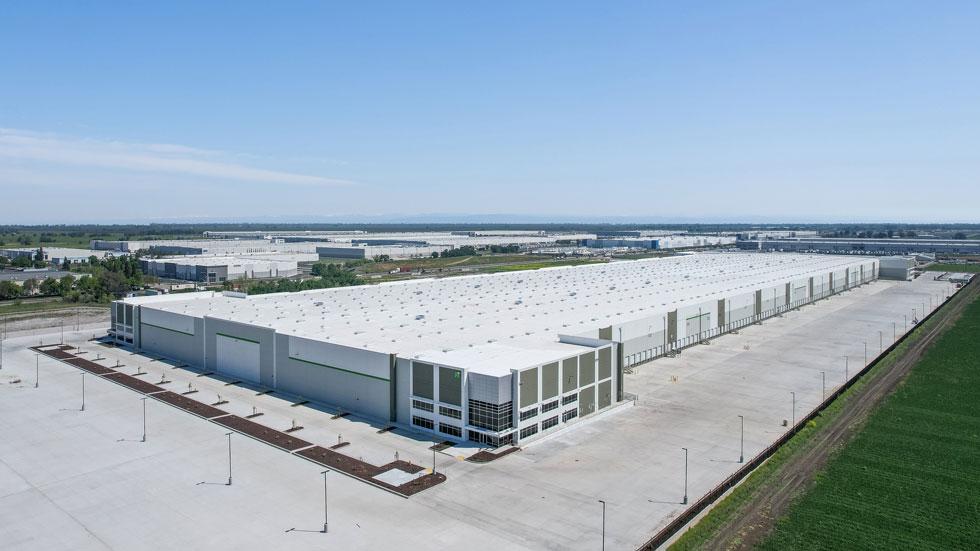
“As natural disasters, regulatory shifts, and unexpected political events loom, executives acknowledge that agility is crucial for determining whether their companies can thrive or falter,” Prologis said in announcing the survey results and releasing its first-ever global supply chain outlook.
SIU’s DeYong said supply chain resilience “is like a rollercoaster.” Whenever a major event like a port strike or hurricane shakes up the supply chain, calls for contingency plans and other measures aimed at bolstering the supply chain grow “because the attention and importance are high,” he said.
“Later, as attention dies down and memories become less vivid, the practical considerations such as reducing the cost of excess capacity and decreasing inventory investment start to take precedence and the pendulum swings toward more efficient, but less resilient, supply chains,” DeYong said.
At least for now, though, industrial REITs and other warehouse owners are paying close attention to reinforcing the supply chain. Professional services firms EY and KPMG say this includes:
- Incorporating risk monitoring into the supply chain
- Nailing down alternative energy sources
- Improving cybersecurity
- Buoying the reliability of data
- Fulfilling customer orders from the “most optimal” hub
Industrial REITs are often the largest, most sophisticated owners of industrial space, said Vince Tibone, head of U.S. industrial and mall research at Green Street. So it’s no wonder that industrial REIT executives routinely ponder supply chain disruptions, including how these disruptions might affect their tenants’ myriad needs.
“Supply chain disruptions strengthen the argument for carrying more inventory onshore, which would boost demand for warehouse space,” Tibone said. “However, given macroeconomic uncertainty and weakening consumer health, many tenants continue to emphasize just-in-time inventory strategies to prevent having too much inventory if internal sales forecasts miss,” he adds.